Getting started with a plasma cutting machine could be a frustrating task, especially for anyone with no prior experience with a mechanical device. If this is your case, give the following instructions a look.
Firstly, we believe that before taking this plasma cutter out for some heavy projects, it will be of great help to have an idea about its fundamental components, its ability as well as its recommended setup.
Plus, since those factors might vary among different types of plasma cutting machines, we suggest that you look through the manual coming alongside the machine to familiarize yourself with the tool – its basic components, functions, etc.
Well, Let’s get down to learn how to set up a plasma cutter right now!
How To Set Up a Plasma Cutter?
Step 1: Choose a suitable working place
Plasma cutter delivers the best results in a dry and clean environment. You can even consider installing some air-dryers in your working space.
Next, pick out a suitable surface for the metal pieces, which will later be sliced apart with the plasma cutter, to lie down comfortably. Look for something that is flat and large enough so that it will not hinder your movements.
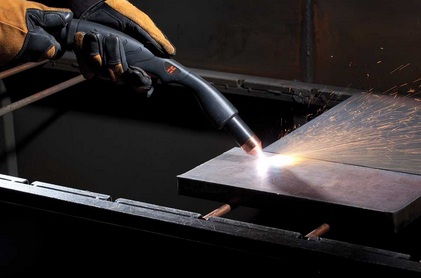
Manual plasma cutting table
The surface should also be placed at a position that you feel most convenient to work with. For the sake of your own safety, check whether the working surface is sufficient to support the weight of your project. Use the metal clamp for fixing the metal pieces to the surface.
Step 2: Plug the plasma cutting machine in
Keep the machine in power-off mode before plugging the machine to an electricity source. The source shall have a suitable voltage outlet (240V or 415V supply, depending on the kind of machine you have)
Warning: Due to the current draw (Amp), this unit should NOT be connected to the standard household of 110V outlets.
Step 3: Attach your plasm cutter to the air compressor
Doesn’t your plasma cutter feature an air compressor? No problem! You can connect it to one. Air compressors work to keep the flow of plasma under high pressure, which ensures the quality and the precision of each and every cut
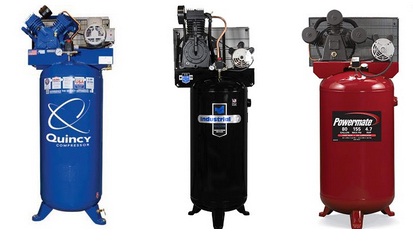
Air compressors
Step 4: Switch the air processor on, then turn on the plasma cutter
Step 5: By using the metal clamp, you can attach the metal that you want to cut to the working surface
To increase the stability of the cutting process, metal clamp is highly recommended.
Step 6: Select the amperage and the travel speed of the torch
The specific number of amp depends on the material, the thickness, etc of the metal piece you want to cut.
There is a simple rule to follow: higher amps for thicker materials, but you could also keep the same amps and adjust the travel speed of the torch. It is quite self-explanatory, but slower travel speed means deeper cuts.
Step 7: Connect the torch to the plasma cutting machine
The torch is a part of the plasma cutter that you directly work with. Make sure that you have this part connected to the machine.
Step 8: Start cutting
Pull the safety device on the torch down and press the trigger on the torch handle to initiate the cuttings. Once you press the trigger, in a flash, it will shoot an arc and start cutting. Steadily drag the torch on the workpiece as a stream of high-degree gas melts the metal.
When you have finished cutting, turn off it by flipping the power button to OFF.
Step 9: Turn off and disconnect the air compressor
Move the lever to its original position to switch off the air compressor.
Step 10: Leave the Torch Cooling Down And Wrap Up All Wires And Hoses
After you are done with the cutting, wait for the torch cooling down. The torch-posting flow air will last for about 20 to 30 seconds, so wait for it to end before putting the torch down.
Disconnect the metal clamp and wrap up the hoses. Wrap up all the lines: airline, the torch, and ground line so they will not get entangled the next time you use the machine.
Conclusion
How to set up a plasma cutter maybe not a mission requiring much effort, but it could save you a considerable amount of time knowing to work with it properly in the first hand.
Especially when today, plasma cutting machines are now considered an irreplaceable tool in every fabrication workshop.
Hope that this post can be of some assistance to you working with that amazing machine!
Leave a Reply